
By Alan Huffman, heterogenous integration business unit director
Supply chain constraints have jumped into headlines in recent years as challenges associated with surging demand and pandemic-related disruptions have turned sourcing strategies upside down. The microelectronics industry has been in the spotlight on numerous occasions owing to major shortages in the automotive industry. This has put a mainstream spotlight on issues known to many industry insiders for years – many key manufacturing technologies for the microelectronics value chain have been entirely offshored. While for years it was an abstract vulnerability — for most, when consumers cannot get products they want or need, it very quickly becomes a household issue with real implications for us all.
As a result, there is growing momentum to “re-shore” many of the microelectronic manufacturing capabilities that migrated out of the United States over the past 20 years. Not only does this help to strengthen the nation’s supply chain capabilities, but it also supports many national security initiatives to ensure that the United States maintains an advantage in microelectronics technologies. This initiative is considered so important that Congress is working on a significant funding program called the United States Innovation and Competition Act. While many of the conversations around re-shoring microelectronics manufacturing technologies center around the most advanced and smallest geometries produced by the likes of TSMC, Intel and Samsung, it also acknowledges that perhaps one of the most striking gaps in our domestic infrastructure is for packaging technologies, which is a segment of the supply chain basically abandoned by major U.S. suppliers.
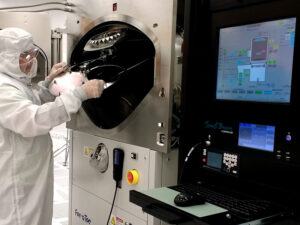
As a country and industry, how did we get here?
Prior to 2000, much of the innovation for advanced packaging came from IDM companies (e.g. IBM, Intel, Motorola) and OSATs (e.g. Amkor, ASE). As the market shifted from high-end computing toward the very high-volume mobile market, cost was the major driver for packaging. This resulted in packaging manufacturing migrating to lower-cost countries, mainly in Asia, while high value innovation resources in the U.S. were focused on advanced node technology development and design for processors.
This led the industry to extend established packaging technologies to accommodate the low-cost objectives of the market, which was achieved very well. Over the last decade, advanced packaging technology advancements began to be driven by leading foundries (TSMC, Samsung, Intel) and OSATs, as packaging technologies have been increasingly relied on to help maintain the pace of performance increase in electronic systems.
In 2016, TSMC introduced a wildly successful fan-out wafer-level packaging, called InFO, that was used by Apple for packaging processors in a low-profile package and is still used in their package-on-package designs for mobile devices today. This example shows the impact of 2.5 heterogenous integration architectures on mainstream applications. Now as we see a slowdown in performance gains by conventional Moore’s Law transistor scaling, the industry is in unanimous agreement that the future of advanced computing will proceed hand-in-hand with heterogenous integration technologies in order to meet the market’s incessant demand for more performance. However, with advanced packaging supply chain infrastructure being virtually non-existent in the U.S., where does that leave us?
The current paradigm shift the industry is fording — taking the industry from the smartphone era to the parallel and edge computing era that will be enabled by advanced hybrid computing architectures. It marks a shift, where packaging technologies previously viewed as non-performance enhancing low-value services, now are critical enablers for system performance, and can create substantial differentiation for products. A significant opportunity exists for the industry and domestic supply chains to re-establish onshore capabilities in technologies that will enable advanced systems in the coming decades.
What SkyWater is doing about it
SkyWater is in the process of implementing three new technology capabilities to establish the company as a domestic leader in heterogeneous integration: silicon interposers, hybrid bonding and fanout wafer level packaging — also known as FOWLP. These platform technologies form the basis of SkyWater’s commitment to establishing leading edge capabilities to support the “More than Moore” generation of microelectronics that the industry will rely on for the future.

Silicon interposers can be thought of as a very advanced circuit board. They utilize silicon microcircuit processes to form multiple layers of routing metal and incorporate through silicon vias, or TSVs, to create an integration platform that allows for extremely short interconnect lengths between the devices assembled to them and provides connections through the silicon to allow for electrical signals to be transmitted from the bottom to the top of the interposer.
Through a technology agreement between Bridg and IMEC, SkyWater is establishing silicon interposer manufacturing in our Florida facility. Interposers are key components used in the integration of multiple devices in very close proximity to one another. High performance computing modules that need intimate integration between logic and memory are an example of an application where interposers play an important role. Interposers are also used for the integration of “chiplets,” which are silicon devices designed to perform a specific function and work together with other chiplets in microsystems.
Bridg is a not-for-profit public-private partnership organization supporting research and development focused on advanced system integration solutions. SkyWater’s silicon interposer technology is based on work done at IMEC, a leading microelectronics research organization in Belgium. In cooperation with Bridg, SkyWater is establishing the manufacturing capabilities to support high-volume silicon interposer fabrication.
Through an agreement with Deca Technologies, developer of the industry-leading FOWLP technology, SkyWater will be establishing the first high-volume FOWLP capability in the U.S. Deca’s first generation FOWLP technology is used extensively in leading mobile applications and their proprietary Adaptive Patterning, with mask-less laser direct imaging lithography, enables high production yields and high-density design rules. SkyWater and Deca are working together to bring Deca’s Gen 2 FOWLP technology to the Florida facility for high-performance computing and networking, artificial intelligence, and edge computing applications. The Gen 2 technology will enable up to 4 routing metal layers with line and space dimensions down to 2 microns and support device die I/O pad pitch down to 20 microns.
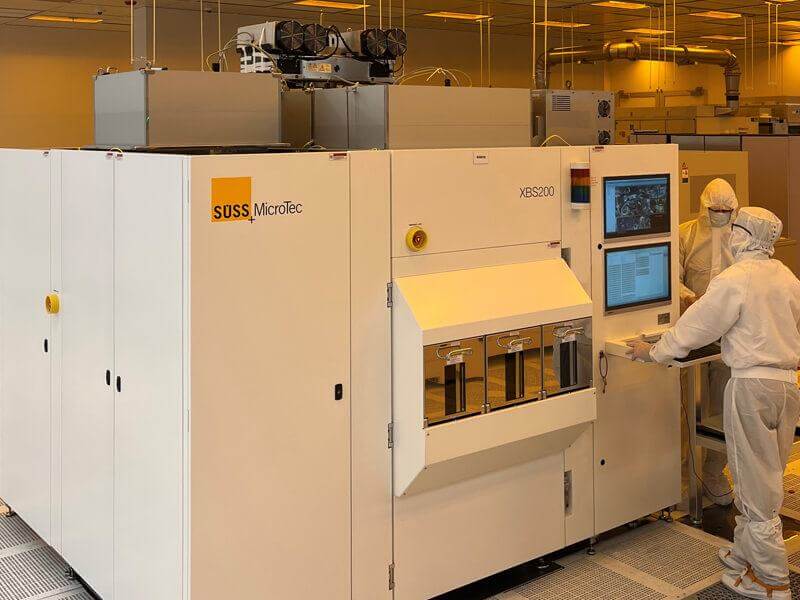
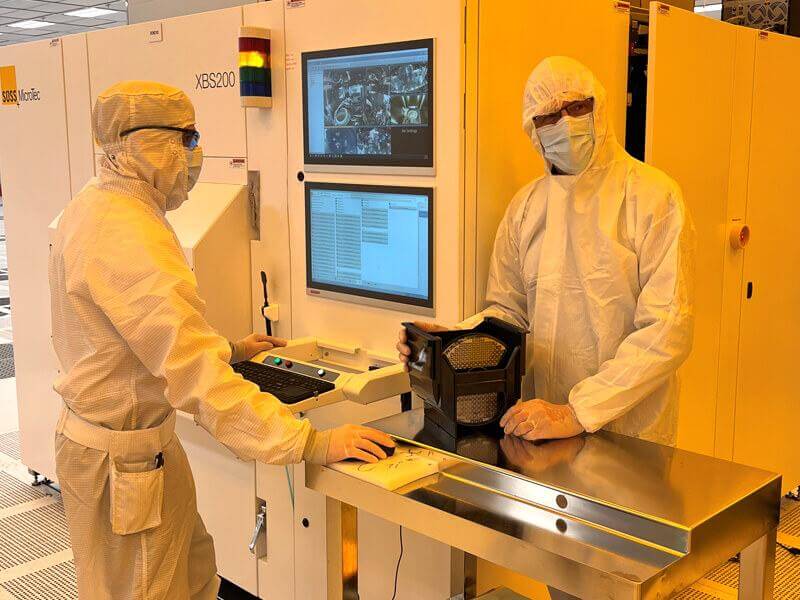
Hybrid bonding is the final heterogeneous integration platform technology that SkyWater is implementing, via a licensing agreement with Adeia (part of Xperi). While silicon interposer and FOWLP are HI technologies that primarily integrate devices in the horizontal direction with vertical off-module signal transmission paths, hybrid bonding enables true 3D integration of devices and allows them to be stacked directly upon each other. This approach allows for very short interconnection lengths between devices, resulting in lower power consumption, higher bandwidth and extremely compact device size.
Through the course of our work enabling disruptive innovators across diverse technology categories, we’ve observed firsthand the need for new back end of line integration architectures in order to maximize device performance. The addition of these advanced technologies to enable 2.5D and 3D architectures provides our customers with a one-stop shop for development and manufacturing services that span front and back end of line technologies and with the IP security of a domestic foundry partner.
With growing market demand for heterogeneous integration and advanced packaging technologies — and broad local, state and national government support for re-shoring them in the U.S. — a great opportunity is presented to the U.S. supply chain for regaining leadership for the next generation of packaging technology. We’re ready for the challenge and looking for partners who are hungry to innovate with us.